On 23 March 2022, Forum Rathenau hosted the fifth hybrid Carbon Cycle Culture Club (C4). This time, experts discussed the prospects for “sugar as a building material”. The event was initiated as part of the structural change programme of the state of Saxony-Anhalt and in connection with the initiative for a New European Bauhaus.
Lignite and sugar are closely linked
Sugar has a long tradition in the city of Zeitz. Beet sugar has been produced here on an industrial scale for over 160 years. Zeitz is also a model city for successful cultural, economic and ecological structural change, which is currently being promoted as the Saxony-Anhalt Project, being part of the New European Bauhaus. The fifth C4 therefore digitally connects the former Zschornewitz power plant with the podium in the former Herrmannschacht briquette factory in Zeitz. “We are currently at the centre of sugar production. Right around us, sugar is being transported in wagons and lorries,” is how presenter Professor Ralf Wehrspohn describes the unusual venue of the C4: the district house of the industrial monument “Brikettfabrik Herrmannschacht“ in Zeitz. A museum in the middle of the industrial site of the Südzucker AG, run by the Central German Environment- and Technology Park Association (MUT). The MUT association is determined to keep Zeitz’s 300-year industrial history alive. The connection between lignite and sugar has existed from the very beginning, as MUT board member Tony Saar explains: “The first director of the Zeitz sugar factory, Richard Herrmann, was also the founder of the briquette factory.“
Zeitz – one of the most exciting places in structural change
“We are here in Zeitz because it is self-evident […]. We are in a city with an incredibly rich history and a deep, shattering structural break in the Wende era“, says Dr. Franziska Krüger, head of the staff unit “Structural Change in the Central German Region”. There is now a unique opportunity to reinvent the city and shape it innovatively. Especially with a partnership like the New European Bauhaus (NEB), a holistic and sustainable structural change can succeed all the better. After less than a year, the NEB network has not only submitted a joint application to the European Commission but can already present the results of the first work phase. In addition, the New European Bauhaus is currently looking into the future of the former ZEKIWA pram factory in the city of Zeitz. “A great area in the centre of the city that can and should be developed structurally,” says Dr Krüger.
The future of the material use of sugar
What can the raw material sugar, the city of Zeitz and innovative cooperation now achieve in the long term? Südzucker AG is a much broader group of companies than its name suggests, says Dr Sebastian Kunz. Sugar is produced here, of course, but also ethanol, for example, represented by CropEnergies AG. Nowadays, the sustainable raw material sugar can be used to produce fuel with ethanol from the company. In addition, sugar beet pulp is already being used as a natural material in the field of building insulation.
Last but not least, the issue of synthetic raw materials is currently in focus. They have increasingly come into disrepute because a carbon base was supposedly considered unsustainable but fossil, and the release of carbon in the form of CO2 is delayed. “How can we create a kind of cycle here so that we don’t have to resort to fossil raw materials?” asks Dr Kunz. The issue of recycling can of course be expanded, but with each pass, there is a decrease in quality. Therefore, Dr Kunz cautions:
“We will not be able to develop a closed-loop with recycling alone.“
One solution may be to extract new carbon from biomass and CO2. Because CO2 is known to be bound within the biomass. With this renewable carbon, carbon cycles can be closed without causing an increase in emissions. The process of photosynthesis is used for this: The sugar plant collects CO2 from the air and uses the sun as an energy source and water as a raw material. In the process, it converts the CO2 into carbohydrates, thus creating a sustainable form of carbon. If materials were created from this procedure and were burnt at the end of their lifetime, this carbon could be returned to the cycle.
Sugar beet is comparatively an exceptionally good agronomic crop because it has the highest yield of usable carbon. “You can equate that with usable carbon,” says Dr Kunz. In addition, sugar beet is a kind of nitrate reducer, as it collects much of the nitrate from the soil. As a deep-rooted plant, it also loosens the soil. In addition, the beet leaf is suitable as a natural fertiliser and the sugar beet is not a host plant for grain pests.
Building shells and furniture made of sugar
Sugar as a building material is also no longer an illusion. Professor Dr Stefan Reich shows pictures of a project by colleagues at the Georgia Institute of Technology, (USA). They used bio-based polyethylene terephthalate (PET) from sugar to make tiles for the shell of a pavilion. An experimental building that shows: “It is possible to construct a building envelope that is largely made from sugar,” says Professor Reich. The path from experiment to approved building material is a long one, he says, but one that can be taken.
“It’s a question of economic viability.”
In the next few years, exciting possibilities will emerge in process engineering, in product development of the chemical industry, which can then be introduced to the construction industry. When asked why these new materials would not be built immediately, Dr. Kunz says: “We are still much more expensive with renewable raw materials today than with petrochemical products.” But interest in renewable raw materials is growing. Professor Reich adds: “Furthermore, in order to bring building materials to the market, extensive testing and certification are required in Europe. The whole process can take several years. The pragmatic way is, therefore, to use new materials in sectors with fewer building regulations, such as interior fittings and cladding or temporary buildings.“
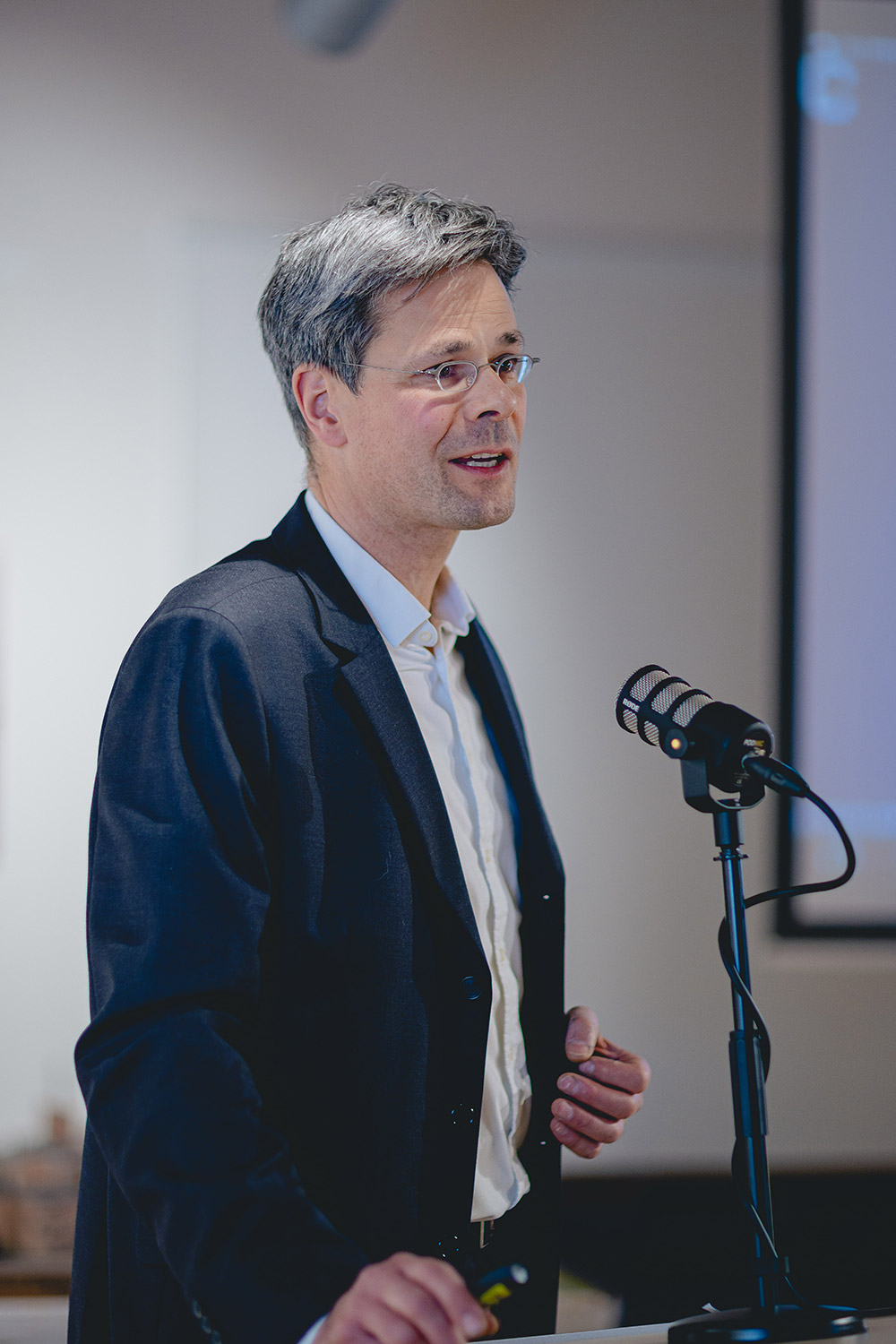
New in the field of insulation materials is the use of fungal mycelia. This refers to thread-like cells of a fungus that could be used as boards or pipe insulation, Professor Reich reports. In the plastics sector, classical bio-based plastics such as cellophane, celluloid and shellac are also used. Modern plastics are very closely linked to the corresponding construction methods, especially in additive manufacturing, 3D printing and granulate exposure – processes that made it possible to work with new mixtures of plastics.
“One interesting mixture, both in composition and feel, is a bio-based polylactide (PLA),” says Professor Reich. Students at Anhalt University of Applied Sciences have used this material to make a stool, a chair and a table, among other things. The production of bio-based PLA takes place through various processes from starch-containing plants such as potatoes, grain, but also sugar. Thus, for example, even load-bearing structures can be produced using 3D printing with bio-based PLA from sugar.
Search for green solutions
In the course of the sustainable structural change in Saxony-Anhalt, gas-processing companies are also looking for green solutions. As a major gas consumer, SKW Stickstoffwerke Piesteritz GmbH is affected by the explosive rise in gas prices, explains Christopher Profitlich. The company produces artificial urea from gas as raw material, converting methane first into ammonia and then into urea. The urea can then be used for fertilisers, but also as a denitrification agent for combustion exhaust gases. The liquid urea solution “AdBlue” is mainly used for exhaust gas reduction for diesel engines of road and rail vehicles.
“If we don’t produce more, a relatively large number of wheels will come to a standstill.”
Gas prices have exploded since last summer. What would happen if SKW could no longer produce fertiliser and “AdBlue”, for example, because of a gas boycott? Profitlich: “If we stop producing, relatively many wheels will stop turning and there will be no more fertiliser.” Without fertiliser, no more plants would grow in the fields in the long term either, as they would extract nutrients from the soil that would have to be replenished with fertiliser.
Of course, SKW is also trying to break away from fossil gas. The issue of green energy is important for the company, but SKW needs gas as a raw material above all. Therefore, solutions are being sought to be able to use natural biomethane from organic processes or synthetically produced methane. But that is still a very long shot.
The future of Zeitz – construction of a CO2 pipeline under consideration
In the future, the Zeitz Chemical and Industrial Park will also play a decisive role in sustainable structural change, as the site already has industrial infrastructures, says Managing Director Arvid Friebe.
One main project is to build a CO2 pipeline from the Crop Energies site in Zeitz to the chemical park. This would make green CO2 available at the Zeitz Chemical Park site. This would also fit in with the green hydrogen that will be available in Saxony-Anhalt in the future. It will come from Leuna via pipeline to the chemical park when the Linde company in Leuna has completed the electrolyser. This would, for example, create the conditions for producing hydrocarbon chains or benzene at the site. If this were combined with a CO2-free infrastructure, many prerequisites would be in place to fulfil the green chemistry agenda. Commenting on this innovative and sustainable transformation in Saxony-Anhalt, Friebe said:
“I think we are on a good path there. We are at the beginning of the road, but the goal has been formulated. We’re off now.”
The C4’s hybrid discussion format on new perspectives for sugar as a building material was recorded live and is available for you to watch as a video stream.
You are currently viewing a placeholder content from Youtube. To access the actual content, click the button below. Please note that doing so will share data with third-party providers.
More Information